New e-waste recycling technology accelerating the circular supply of precious metals
By Tamanna Wadhwani 24 August 2023
Mint Innovation employ green chemistry and natural biomass to recover precious metals from e-waste, with the capacity to recover an estimated AUD $45 million in gold and copper from their Sydney facility every year.
Mint Innovation, a clean technology company, have devised an inventive approach for recovering precious metals from waste, using natural biomass and green chemistry.
Their technology, which is now deployed at a commercial scale, involves a hydrometallurgical method where waste metals are milled into a sand consistency. They then use a proprietary biomass to target and separate specific precious metals like gold, palladium and platinum from the resulting material.
Mint estimate their technology could save around 91 per cent of the carbon that is produced during conventional mining and smelting of metals like gold, while requiring just two per cent of the power and water per kilogram of gold yield.
The company's newly established Western Sydney facility has the capacity to process approximately 3,000 tonnes of printed circuit board (PCB) waste every year, recovering about AUD $45 million worth of gold and copper. This will see up to half a tonne of gold and up to 1,000 tonnes of copper returned to the Australian economy for reuse. The ability to recover copper, which is present in high amounts and serves as the conductive links between circuit components, is a significant benefit of the facility.
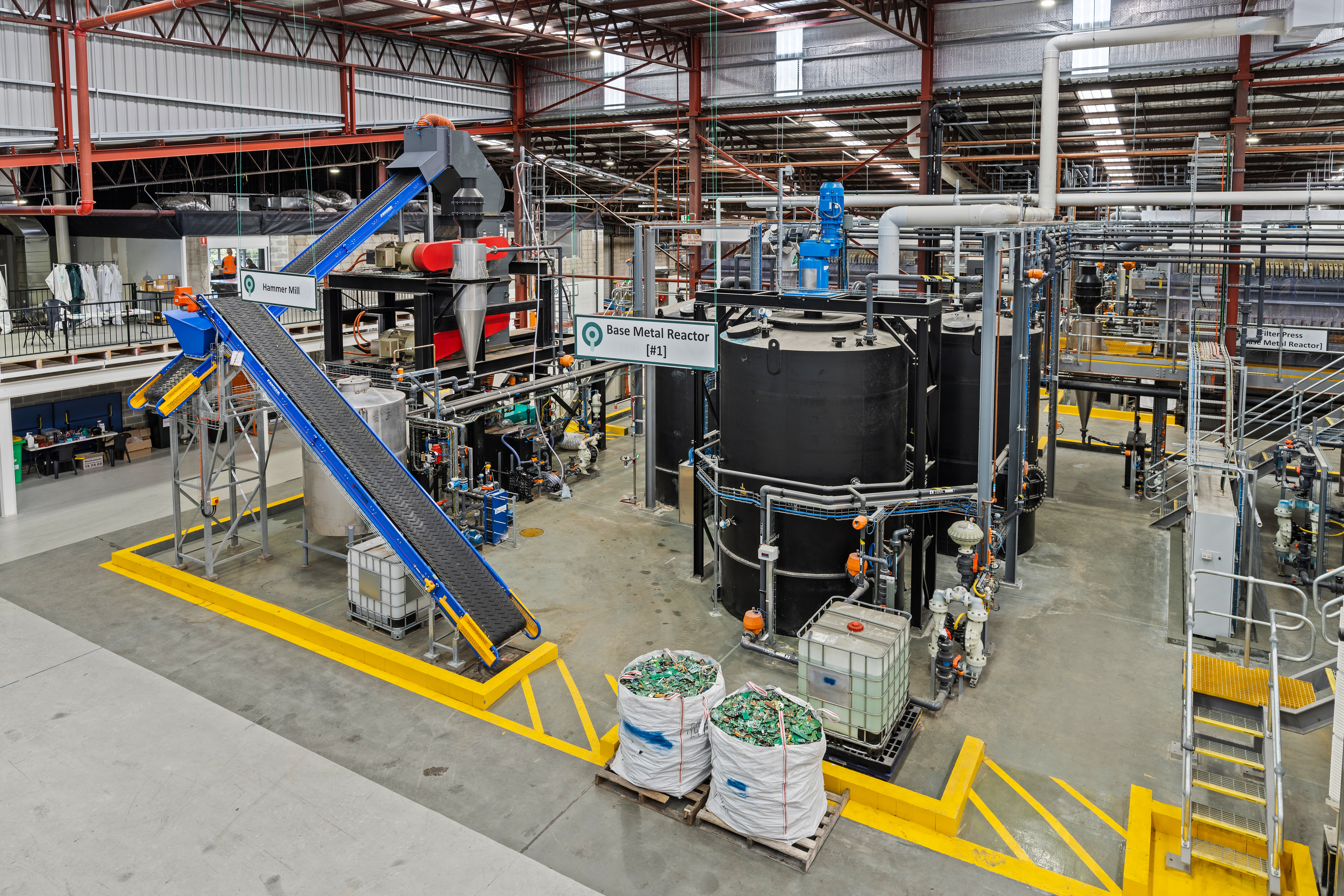
After extracting the metals from circuit boards, some secondary materials like plastic and ceramic get left behind, which are unaltered through the process other than being broken down into granular form. Mint is working on incorporating these into new plastic materials such as fence posting, plasterboards (for gypsum), or an aggregate replacement in the construction of roads and other civil works.
Will Barker, CEO at Mint Innovation said their technology’s footprint is sophisticated and safe enough for city deployment.
“A ‘city-scale’ solution means we can deal with the waste near its collection point and avoid transportation and shipping emissions. This also stops hazardous waste from being sent to landfill or shipped to other countries where informal metal recovery creates well-documented environmental and humanitarian issues,” said Barker.
The company’s founders Dr Will Barker and Ollie Crush, who set out on a mission to make waste-to-value solutions economically viable and scalable, focused their efforts on extracting very high-value products from very low-value waste streams.
Dr Ollie Crush identified a suite of biological materials to selectively recover gold and other precious metals from complex mixed materials, and this was first proven in a test tube experiment before demonstrating in a facility at East Tamaki. With increased rounds of funding over a period of six years, the team was able to commercially scale this solution to processing ten tonnes of e-waste a day and successfully established their facility in Sydney last year.
With e-waste being one of the fastest-growing waste streams in Australia, Mint’s technology could provide a much-needed solution to prevent potentially hazardous materials from entering landfill and recover precious materials in large quantities from existing urban mines.
Learn more about their technology by visiting Mint Innovation.
Tamanna moved from India to Australia to pursue a degree in environmental science and conservation biology. After learning about the concept of a circular economy in 2020, she worked with various organisations in this sector and is interested in solving complex climate change and waste management problems. She loves to communicate with people about all things sustainability or animals. Outside of work, Tamanna is a budding hip hop dancer who also loves travelling, cat cuddles and reading.